Decoding Carbon Black and Its Crucial Role in the Rubber Industry
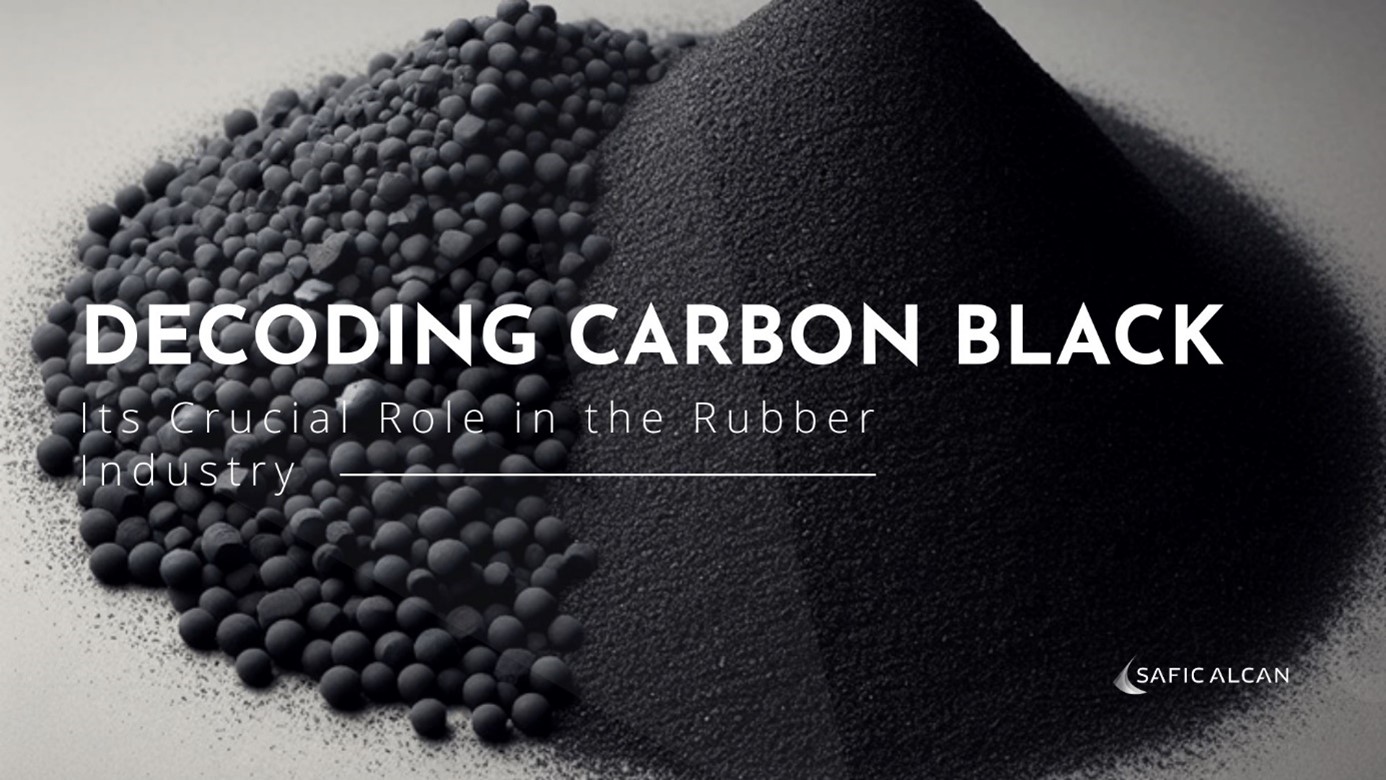
Explore the evolution of carbon black, from ancient pigments to modern engineering, and understand its crucial role in rubber compounding. Discover diverse manufacturing processes, key properties, and sustainability initiatives shaping the future of carbon black and the rubber industry as a whole.
Most formulators might not be aware that a staggering 90% of global carbon black production is dedicated to rubber applications, encompassing both tires and non-tire applications (hoses, seals, gaskets, conveyor belts, etc.).
The remaining 10% finds utility as a pigment, UV stabilizer, antistatic, and conductive agent in various industries such as plastics, inks, and coatings applications. This article navigates through the evolutionary journey of carbon black, tracing its roots from ancient pigments to its contemporary engineered forms.
By examining the manufacturing processes and carbon black's key properties, the article sheds light on understanding its pivotal role in reinforcing rubber. The exploration concludes by spotlighting ongoing industry efforts to tackle sustainability challenges through the development of environmentally friendly alternatives. Promising sources of sustainable carbon black include those derived from tire recycling processes and methane pyrolysis.
Journey Through Time: The Origins and History of Carbon Black
In prehistoric times, carbon-based black pigments were used for drawing, traditionally produced by charring organic materials like wood or bone.
Charcoal horse drawings Chauvet cave - France
Ancient Chinese and Egyptian civilizations employed soot mixed with biobased substances for writing letters, obtained by allowing a flame from a vegetable oil lamp to contact a cooled surface, forming the precursor to the lamp black method.
This method laid the groundwork for subsequent processes like channel and gas black, both utilizing gas flames on cooled surfaces. In the late Greco-Roman era, substantial amounts of carbon black were in demand for creating inks and mural paints.
The primary method employed was the lampblack process, but this time, resin from pine trees was used as a new feedstock. Despite their historical association, these early lamp blacks exhibit notable differences in both chemical composition and physical properties when compared to modern engineered forms. Today, carbon blacks are 95% to 99% pure elemental carbon (12C) in the form of colloidal particles with a high surface-area-to-volume ratio.
Evolution in Rubber: Carbon Black's Crucial Role
Mr. S.C. Mote's innovation in the 1910s and the growth of the carbon black industry.
Charles Goodyear, the American inventor of the vulcanization process, patented the use of carbon black in rubber as a pigment in the 1840s. However, as history goes, it wasn't until the 1910s that the enhanced abrasion resistance of natural rubber with carbon black was reported by an Englishman, Mr. S.C. Mote, surpassing mineral oxides (ZnO or PbO), the early semi-reinforcing fillers at the time. The carbon black industry saw significant growth, with the 1920s witnessing the rubber industry consuming only 40%, compared to the remarkable 90% a century later. the rubber industry consuming only 40%, compared to the remarkable 90% a century later.
During the first half of the 20th century, channel blacks were mainly produced in the USA, driven by abundant and affordable natural gas feedstock. In contrast, Europe explored alternative procedures, leading to the successful 1934 development of the gas black process in Germany by Degussa (the predecessor to Orion Engineered Carbons).
The gas black process, similar to the channel process, relies on thermo-oxidative decomposition but uses vaporized oil, primarily coal tar distillates. In the 1940s, Phillips Petroleum introduced the oil furnace process, producing the first semi-reinforcing black, FEF (N550). This innovation allowed the adjustment of both critical parameters: particle size and, henceforth, structure. Since the 1960s, the more efficient oil furnace black process has dominated, constituting over 98% of global carbon black production today.
How Is Carbon Black Manufactured?
Explore the major production processes, from the Lamp black method to the MMM black process.
Most industrial carbon blacks are produced through the principle of 'incomplete combustion' of hydrocarbons, in the presence of oxygen, under controlled conditions. The five major commercially recognized production processes are:
- Lamp black process – pioneering production method.
- Channel black process – developed in the 1870s in the U.S.
- Degussa gas black process – developed in the 1930s in Germany.
- Furnace black process – developed in the 1940s in the U.S.
- MMM black process – developed in the 1980s in Belgium.
A second method is also employed, namely that of 'thermal decomposition,' during which carbon black is formed in the absence of oxygen. The two major commercially recognized production processes are:
- Acetylene black process by cracking acetylene gas – developed in the 1920s in Germany.
- Thermal black process by cracking natural gas or oil – developed in the 1930s in the U.S.
Microscopic Marvel: Examining Carbon Black Under the Electron Microscope
Delve into the microscopic world of carbon black's aggregates and particles.
Carbon black is commercialized in the form of finely divided black beads or powder. On a microscopic scale, its characteristics become even more fascinating. The basic components of carbon black are aggregates, with sizes varying from a few hundred nanometers, and these are the smallest dispersible units (i.e., they are hardly affected by the mixing process).
An aggregate of carbon black is formed by the interpenetration (fusion) of nearly spherical elementary particles, with sizes varying from a few tens of nanometers. Each elementary particle consists of the arrangement of small graphitic platelets visible in high-resolution electron microscopy. The arrangement of these graphitic platelets is highly disordered, giving carbon black a paracrystalline construction. These small-sized platelets create a multitude of scales on the surface of the particles, forming a turbostratic structure.
On a macroscopic scale, these aggregates join through van der Waals forces to form agglomerates, ultimately resulting in the commercialized carbon black product in the form of powder, beads, or pellets (with a size of 1-2 mm).
Properties Unveiled: Morphology and Characteristics of Carbon Black
Understand the key features, including particle size, structure, aggregate size, and surface energy.
- Particle size: defined by the average diameter of the particles that make up the aggregate. The smaller the particle size of carbon black, the finer the carbon black. Primary particles may contain pores, referred to as porosity, which explains why, in a number of cases, surface area measurement is not strictly inversely proportional to the diameter of the particle.
- Structure: referred to the arrangement of these particles within the aggregate. The more twisted the shape of the aggregate, the more structured the carbon black is considered.
- Aggregate size: formed when loose aggregates come together. Aggregate size and their distribution can vary. The smaller the aggregate size of carbon black, the finer the carbon black, but it is essential not to confuse both, as these properties are not always correlated.
- Surface energy: influenced by the physical arrangement of graphitic platelets and the presence of various chemical groups, including carboxyl, hydroxyl, quinonyl, lactone, and derivatives. Carbon black, comprising 95% to 99% elemental carbon, also contains elements such as oxygen, hydrogen, nitrogen, and sulfur. Except for sulfur, these elements are primarily located on the surface of carbon black.
Rubber Compounding Mastery: The Role of Carbon Black
Explore the toolkit of formulation ingredients and the impact of reinforcing fillers on rubber compounds.
In the toolkit of formulation ingredients, rubber engineers have incorporated fillers into rubber compounds for decades, driven by two primary objectives:
- Reducing formula costs via a dilution effect.
- Enhancing mechanical properties via a reinforcing effect.
There is no precise definition of the term 'reinforcing,' but it can be translated to a substantial increase in the lifespan and improving the performance of rubber products (industrial rubber goods, hoses, belts, etc.) or tires. By adding a reinforcing filler, two fundamental modifications are made:
- Elastomer is replaced by undeformable filler particles.
- Elastomer-filler interfaces are developed.
At the interface, the polymer becomes immobilized and appears rigid due to its bonding with the filler particles (The so-called 'bound rubber' appears during the mixing of the elastomer and fillers). As a result, these fundamental modifications have two revealing effects on the rubber compound properties:
- An increase in tensile strength.
- An increase in stiffness throughout the force-elongation curve.
This phenomenon is observed regardless of the type of elastomer. Even with unfilled natural rubber (NR), deformation amplification occurs but with a much less pronounced effect as the NR is capable of crystallizing under tension.
Eco-Friendly Innovations: Addressing Sustainability Challenges with Carbon Black
Discover innovative approaches such as recycling and methane pyrolysis to make carbon black more sustainable.
In response to growing environmental concerns, the demand for eco-friendly carbon black is on the rise, driven by the need for sustainable alternatives to conventional production methods. Below, innovative approaches and processes are presented:
Carbon black from recycling: the pyrolysis process is applied to treating end-of-life tires (with the principle applicable to any rubber waste), aiming at the recovery of two essential raw materials: (i) carbon black and (ii) oil.
(i) The first approach results in the extraction of the recovered carbon black (rCB), with a carbon footprint 70 to 80% lower compared to virgin carbon black.
(ii) The second approach involves further processing the recovered oil. The BlackCycle consortium, led by Michelin, achieved a groundbreaking milestone by producing the world's first sustainable carbon blacks (sCB) for tires. This innovative process uses oils from end-of-life tire pyrolysis in a conventional carbon black furnace reactor, maintaining crucial properties in rubber compounds. #OrionEngineeredCarbons is the only carbon black producer involved in the BlackCycle project.
Carbon Black from methane pyrolysis: this process, aimed at producing hydrogen, offers a low emissions profile by generating solid carbon instead of carbon dioxide. The use of bio-sourced methane and an all-electric production process enhances sustainability.
Supporting you in designing sustainable Rubber formulations
Tracing its evolution from ancient pigments to modern engineered forms, we have explored the diverse manufacturing processes of carbon black and its key features, with an emphasis in the pivotal role of carbon black in reinforcing rubber, enhancing mechanical properties, and improving the durability of rubber products.
It is important, however, to not shy away from the key sustainability challenges in the rubber industry, finding and showcasing innovative approaches to make carbon black more sustainable such as tire recycling and pyrolysis of bio-sourced methane. These eco-friendly alternatives aim to reduce environmental impact and shape the future of carbon black and the rubber industry as a whole.
At Safic-Alcan our technical experts will always ensure to streamline innovative and sustainable solutions for your carbon black enabled formulations.
To discover more, visit our online catalog.