Knowing your resins: Choosing the right resin for different market applications.
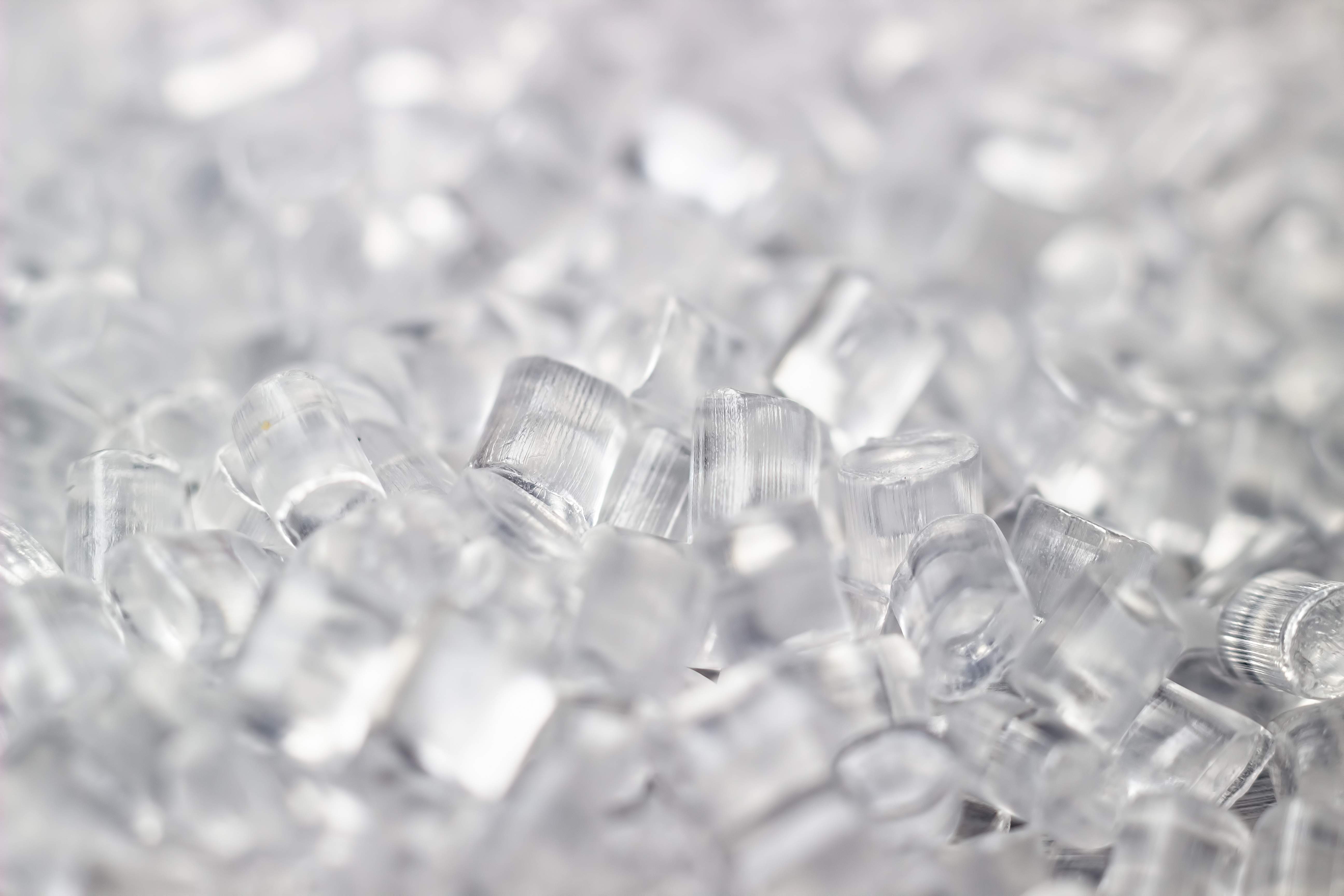
We have created this useful guide to help you choose the right resin for different market applications. Want to find the perfect resin to your formulations?
Which resin, for which application?
Resin is a highly viscous chemical compound that when cured under certain conditions becomes irreversibly hard.
True resin is an organic substance sourced from the bark of trees, especially pines, spruce, and firs. These are soluble in various organic liquids, except water.
Natural resins are mainly used for the manufacture of varnishes, adhesives, food glazing agents, incense, and perfumes.
For most of the industrial applications today, however, synthetic resins are used that have several classes depending on how they are manufactured (by esterification and/or polymerization of organic compounds).
Thus, choosing the right resin for a particular application becomes a pivotal decision for the manufacturers, since there is no “one size fits all” solution. Specifying the correct resin for your application will ensure that your finished product meets its performance requirements.
Polyester Resins
Polyester resins are high-density polymers formed by the combination of polyhydric alcohols and dibasic organic acids. They are highly flexible, heat-resistant, flame-resistant, and chemical-resistant as well. Polyester resins are the least expensive of resin options and, therefore, are used to process large quantity products.
Applications include:
• Construction equipment • Aircraft components
• Auto body fillers • Marine components
• Fishing rods • Coatings
• Skis • Bottles
• Laminate • Decorative accessories
Polycarbonate Resins
Polycarbonate resins are thermoplastic polymers mainly manufactured by polymerization of phosgene and bisphenol A.
They are transparent, impact-resistant, stain-resistant, heat-resistant, and feature excellent toughness and thermal dimensional stability.
Thus, polycarbonate resins are mainly used for applications that need to maintain their strength even in stressful conditions. They also have a high refractive index.
Applications include:
• Safety helmets • Ophthalmic lenses
• Security windows • Photography films
• Automotive headlamps • Skylights
• Motorcycle face shields and windscreens • Anti-vandal glazing
• Safety goggles • Metal replacements
Polyurethane Resins
Polyurethane resins are copolymers manufactured from polyol and isocyanate components. They are extremely versatile and can be used to manufacture a wide range of different products when combined with other resins.
They offer excellent adhesion to substrates. Other notable characteristics of polyurethane resins include high elasticity and a good balance of elongation and hardness.
Applications include:
• Surface coatings and sealants • Foam liners for clothing
• Insulation panels • Stretchable fabrics
• High-performance adhesives • Hard plastic components
• Elastomeric tires and wheels • Temporary implants
• Carpet underlay • Upholstery cushioning
Epoxy Resins
Epoxy resins are thermoset polymers mainly developed by polymerization of epichlorohydrin and bisphenol-A.
They have extensive industrial and consumer applications, owing to their outstanding properties such as heat resistance, chemical resistance, electrical insulation, high adhesive strength, higher dimensional stability, and toughness.
Applications include:
• Structural adhesives • Fiber-reinforced plastics
• Crash-resistant adhesives • Rigid foams
• High voltage insulator materials • Industrial coatings
• Paints • Thermal interface materials (TIMs)
• Primers and sealers • Aerospace and marine applications
Polystyrene Resins
Polystyrene resins are hydrocarbon polymers manufactured from the monomer styrene, a petroleum-derived aromatic liquid.
They have a high refractive index, good electrical insulation properties, and good dialectic strength with outstanding resistance to salts, acids, and alkalis.
Polystyrenes are clear, low-cost resins that are easy to manufacture.
Applications include:
• Disposable food service ware • Toys
• Instrumentation hosings • Gardening pots
• Cooling towers • Pipes
• Insulating panels • Laboratory ware
• Automotive instruments • Rubber
Phenolic Resins
Phenolic resins, called by the tradename Bakelite, are thermoset polymers formed from a combination of phenol and formaldehyde.
Its properties include heat resistance, electrical resistance, chemical resistance, corrosion resistance, good dimensional stability, hardness, and durability.
Phenolic resins can be easily molded into a variety of shapes and complex structures, making them adaptable for use in 3D printers as well. Phenolic resin countertops present a great resistance to bacteria and fungi as well.
Applications include:
• Brake linings • Automotive ashtrays
• Cookware and stove handles • Adhesives for cement
• Resin impregnation • Motor brush holders
• Laminate • Bonded adhesives
• Electrical components • Molds
Silicone Resins
Silicone resins are three-dimensional cross-linked polymers often formed with the less reactive tetraethoxysilane (TEOS) or ethyl polysilicate and several disiloxanes.
They form hard films with excellent weathering resistance, heat resistance, water repellency, oxidative stability, and dielectric properties. They also display low surface tension, and retention of elasticity, even at low temperatures.
Applications include:
• Encapsulated resins •Wire varnishes for high-performance electric motors and generators
• Bakeware • Defoamers
• Fireplace inserts • Rubber
• Laminating and molding • Silicone enamels and paints
• Protective coating resins • Water-resistant applications
Acrylic Resins
Acrylic resins are transparent thermoplastics formed from acrylic acid, cyanoacrylic acid, methacrylic acid or other related compounds.
They have good tensile strength with UV resistance, weather resistance, water resistance, and impact resistance properties. Due to their excellent weatherability as coating materials, they are extensively used for automotive, plastic, and architectural coatings.
Applications include:
• Adhesives • Architectural wall paints/masonry
• Structural and decorative panels • Translucent tiles
• Elastomers • Tooth restorations
• Industrial and architectural coatings • Finishing varnishes
• Signs • Marine paints
Polypropylene Resins
Polypropylene resins are colorless, low-density polymers that don’t contain bisphenol-A. They have excellent thermoforming and injection molding properties.
Since they have good heat resistance and chemical resistance, they can be sterilized and, thus, are often used for making medical grade equipment, including disposable syringes, petri dishes etc. Polypropylene resins are easily processed and moldable.
Applications include:
• Toys • Fibers and filaments
• Plastic furniture • Coatings
• Electronic components • RSpecimen bottles
• Medical vials and syringes • Disposable food service ware
• Pipe and production tubing •Packaging for products
Polyethylene Resins
Polyethylene resins are the most common type of resins, commercially produced with a wide range of specifications. They can be categorized into low density (LDPE), high density (HDPE), and ultra-high molecular weight (UHMW-PE) groups.
Polyethylene resins have a high degree of flexibility. They also have excellent moisture resistance, chemical resistance, and steam resistance.
Applications include:
• Packaging for laminates and films • Toys
• Food packaging • Molds
• Containers • Garbage containers
• Cable insulation • Pipes and fittings
• Coatings • Medical devices
Key considerations
When choosing the right resin for your application, clearly understand the physical requirements of the product, including environmental conditions, potential stressors, chemical exposure, and its expected service life.
These are the most crucial factors in creating the perfect product design.
Different resin classes have different values of tensile strength, durability, flexural modulus, elongation, and resistance to heat, chemicals, corrosion, moisture, impact, etc.
So, the type of resin you choose for your application largely depends on the desired application outcome.
Will the parts be exposed to chemicals? Will they be exposed to extreme temperatures? Is particular or transparency required? How string the part should be? Does it need to be flexible or elastic? Will it be able to withstand impact?
Resins also fall into different grades, including commodity resin grade, engineering resin grade, and specialty/high-performance resin grade.
- Commodity resin grades are inexpensive plastics typically produced at a high volume. Due to their low cost, they are used for making common consumer goods where mechanical strength doesn’t matter much. 
- Engineering Resin grades have better mechanical and thermal properties than commodity resins. They offer good resistance to chemicals, high temperatures and corrosion. They are commonly used as a potential alternative for metal parts.
- Specialty/High-Performance Resin Grades are extremely strong, tough and dimensionally stable. They have excellent chemical resistance, radiation resistance, long term thermal stability and good mechanical properties. Thus, they can be used for extremely demanding and critical use applications, like surgical instruments and coal boilers.
The choice of resin also depends on its cost and quality.
While this guide gives you a general overview of which resin type is suitable for which application, the ultimate decision comes down to balancing the considerations that are most critical to product design.
How does your budget balance against your performance needs? How does your aesthetic goals balance against the need for durability and strength?